Hot-Dip Galvanized Steel: The Superior Choice for Corrosion Protection
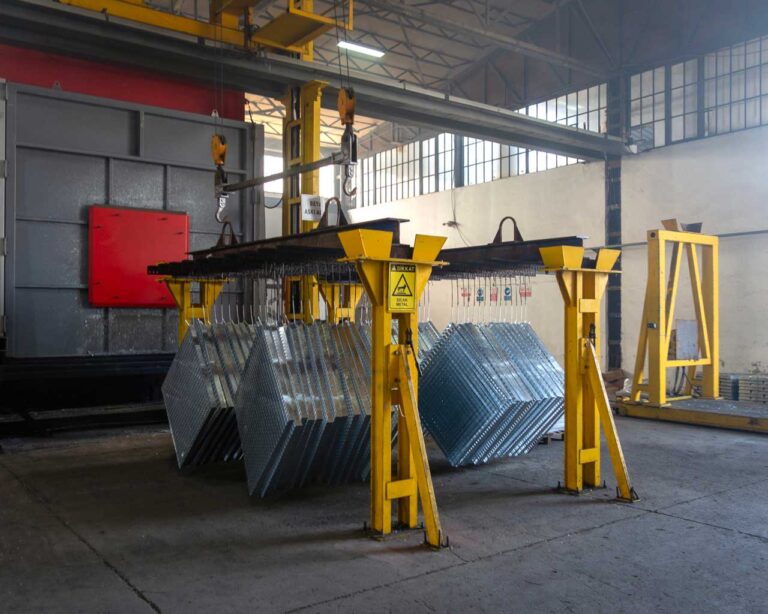
Key Takeaways
- Hot-dip galvanized steel provides superior long-term corrosion resistance compared to other coating methods
- The metallurgical bond created during the hot-dip process results in a thicker, more durable zinc coating
- Ideal for construction, outdoor structures, and industrial applications where durability is essential
- While slightly less uniform in appearance than electro-galvanized steel, hot-dip galvanized steel offers significantly longer service life
- Intsel Steel East provides premium galvanized steel products for all your project needs
Understanding Hot-Dip Galvanizing: Process and Benefits
Hot-dip galvanizing is a time-tested method of protecting steel from corrosion by immersing it in molten zinc. This process creates a metallurgical bond between the zinc and steel, forming layers of zinc-iron alloys topped with a layer of pure zinc. The result is a coating that doesn’t just sit on the surface but becomes an integral part of the steel itself.
The Hot-Dip Galvanizing Process
The hot-dip galvanizing process involves several critical steps:
- Surface Preparation: The steel is thoroughly cleaned to remove all oils, greases, dirt, and mill scale through degreasing, pickling, and fluxing.
- Immersion: The prepared steel is dipped into a bath of molten zinc heated to approximately 840°F (450°C).
- Metallurgical Reaction: During immersion, zinc and iron interact to form zinc-iron alloy layers.
- Cooling and Inspection: After withdrawal, the steel is cooled and inspected for coating quality and thickness.
This process creates a robust protective barrier that shields the underlying steel from corrosive elements, significantly extending its service life.
Hot-Dip vs. Electro-Galvanized Steel: Understanding the Differences
When comparing galvanization methods, it’s essential to understand the fundamental differences between hot-dip and electro-galvanizing to select the right material for your specific application.
Coating Thickness and Durability
Hot-dip galvanizing typically produces a zinc coating thickness of 1.7-3.4 mils (43-86 microns), while electro-galvanizing creates a much thinner coating of 0.2-0.7 mils (5-18 microns). This substantial difference in thickness translates directly to corrosion protection capabilities.
The thicker coating provided by hot-dip galvanizing offers:
- 3-5 times longer corrosion protection than electro-galvanized steel
- Superior protection in harsh environments, including coastal areas
- Greater resistance to mechanical damage during transport and installation
Surface Finish and Appearance
Hot-dip galvanized steel typically has a distinctive crystalline pattern known as “spangle.” While this finish is less uniform than the smooth surface of electro-galvanized steel, it offers superior protection where durability matters more than cosmetic appearance.
For applications where appearance is secondary to longevity and performance, hot-dip galvanizing is the clear choice.
Applications: Where Hot-Dip Galvanized Steel Excels
Galvanized steel is the preferred choice for numerous applications where long-term corrosion protection is critical:
Construction and Infrastructure
- Structural steel beams and columns
- Highway guardrails and safety barriers
- Bridge components and supports
- Transmission towers and utility poles
- Lighting poles and traffic signal structures
- Solar panel mounting systems
Industrial Applications
- Storage tanks and pressure vessels
- Pipe systems for water, gas, and chemicals
- Industrial equipment frames and components
- Material handling equipment
- HVAC equipment and ducts
- Outdoor staircases and platforms
- Agricultural buildings and equipment
These applications benefit from hot-dip galvanizing’s exceptional durability, minimal maintenance requirements, and long service life – often 50+ years in many environments.
Cost-Effectiveness: The Long-Term Value Proposition
While the initial cost of galvanized steel may be higher than some alternatives, the long-term economics strongly favor this solution:
- Reduced Maintenance: Hot-dip galvanized steel requires virtually no maintenance for decades.
- Extended Service Life: Many hot-dip galvanized structures remain in service for 50+ years without recoating.
- Lower Lifecycle Costs: When calculated over the full service life, hot-dip galvanizing typically proves more economical than painting or other coating systems.
A lifecycle cost analysis often reveals that hot-dip galvanizing can save 15-40% compared to regularly maintained painted steel over a structure’s lifetime.
Environmental Sustainability
Hot-dip galvanized steel aligns well with sustainability goals:
- Durability: Longer service life means less frequent replacement and reduced resource consumption.
- Recyclability: Both zinc and steel are 100% recyclable without loss of properties.
- Energy Efficiency: The energy invested in galvanizing is offset many times over by the extended service life.
- Zinc Recovery: Modern galvanizing operations recover and reuse zinc, minimizing waste.
Intsel Steel East: Your Partner for Premium Hot-Dip Galvanized Steel
At Intsel Steel East (formerly Bushwick Metals), we pride ourselves on providing high-quality galvanized steel products that meet the demanding requirements of construction, industrial, and manufacturing applications.
Our comprehensive inventory includes:
- Galvanized steel angles in various sizes and specifications
- Galvanized steel beams and channels
- Galvanized flat bars and plates
- Custom-cut galvanized steel to your exact specifications
With decades of experience serving the Northeast region, our team of experts can help you select the right galvanized steel products for your specific project requirements.
Conclusion: Making the Right Choice for Your Application
When durability, longevity, and reliable performance are paramount, hot-dip galvanized steel stands as the superior choice. While electro-galvanized steel has its place in applications where a smoother finish or better paintability is required, hot-dip galvanizing remains the gold standard for corrosion protection in demanding environments.
For construction projects, infrastructure components, and industrial applications where failure is not an option, galvanized steel delivers unmatched value and performance.
Contact Intsel Steel East today to discuss your hot-dip galvanized steel requirements and discover why we’ve been the trusted steel supplier for the Northeast region for decades.