High Carbon Steel Vs Low Carbon Steel
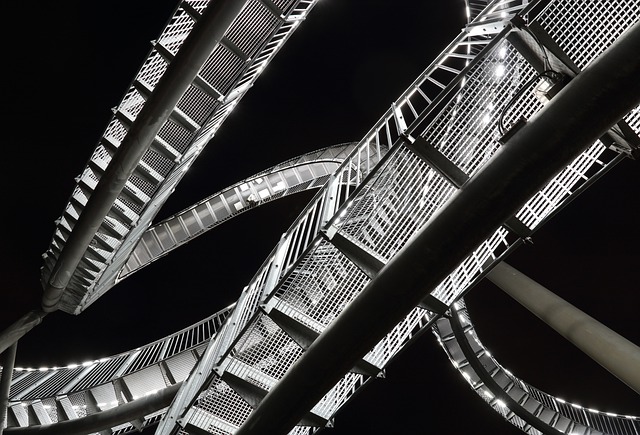
Whether you’re an avid collector of knives and swords or an industry professional (or maybe both), you’ve probably seen the terms “high carbon steel” and “low carbon steel” thrown around quite a bit. But you may be at a loss regarding the exact relationship between carbon and steel.
What exactly is the stuff from an unassuming, dark and crumbly lump of coal actually doing in a chef’s knife or steel beam anyway? And why does it matter how much of it is in there? By the end of this article, you’ll know all you need to about high carbon vs. low carbon steel, and why this abundant earth element is so crucial in our world’s most widely used metal. So just keep reading!
What Is Carbon Steel?
On its own, iron is a relatively soft, ductile metal. It is also highly prone to oxidation (rusting). However, iron’s softness and susceptibility to corrosion are greatly mitigated by the inclusion of carbon via a process called smelting.
This yields a material called pig iron, whose extremely high levels of carbon make it much too brittle for any practical applications. Thus, steps are then taken to lower the pig iron’s carbon content (decarburization) to desired levels (below 2.1%), resulting in steel.
Now, you may have picked up on the fact that, by definition, steel is an alloy of iron and carbon. So how is “carbon steel” not a redundant term? And what sets it apart from other steels?
According to the American Iron and Steel Institute (AISI), carbon steel must contain up to 2% carbon, no more than 1.65% manganese, 0.6% silicon, and 0.6% copper, and no less than 0.4% copper.
In other words, almost all steel used today is in fact carbon steel. The real difference in quality and optimal uses for different variants of carbon steel lies in how they’re blended with other metals, including carbon, and to what percentages. For this reason, high carbon, medium carbon and low carbon steels are unique mixes of iron, carbon and other metals to give each distinct hardness properties that carbon content alone doesn’t offer.
High Carbon Steel Vs Low Carbon Steel
The AISI reported that carbon steels account for more than 85% of the steel that the United States produces and ships. There are countless individual grades of carbon steel, and each has its own unique qualities and uses. Some of the most popular include:
- 12L14 (highly magnetic with lead added to increase machinability)
- A36 (used for automobile components and building structures like steel beams)
- 1008 (extremely low carbon content and tensile strength; easy to weld)
- 1045 (high strength and hardness)
- 1095 (along with 1045, most popular steel for functional sword and knife production)
Now that we’ve clarified what carbon steel is in a general sense, let’s take a look at what the different levels of carbon mean for the steel itself and how they break down by amounts of carbon, other metals and use cases.
Ultra-high Carbon Steel
The type of steel with the very highest carbon content on the commercial and consumer markets is called ultra-high carbon steel. It’s often considered an experimental alloy and offers a carbon content of 1.25-1.7%. While there’s some overlap between the kinds of items that can be made from ultra-high carbon steel and normal high carbon steel, the ultra-high blend is unique enough to deserve its own category. This type of steel is enormously hard but also too brittle for many industrial or large-object uses. It does however work wonderfully for smaller specialty tools such as:
- High-end chef’s knives
- Modern sword reproductions for martial artists and collectors
- Other cutting tools
- Hammer heads
- Punches
- Dies
High Carbon Steel
Also known as carbon tool steel, high carbon steels contain between 0.6% and 1.2% carbon and manganese levels that vary between 0.3% and 0.9%. Steel with a carbon content any higher than 1.7% (but less than 2%) is technically considered cast iron unless specially heat treated, tempered and blended with chromium or manganese.
High carbon steels enjoy a fair range of applications, such as in:
- Springs
- High-strength wires
- Masonry nails
- Cookery
- Radiators
- Lampposts
Medium Carbon Steel
Of course there’s a mid-range category of steel that sits between the ultra-high and high carbon steel types and their low carbon counterpoint. This is called medium carbon steel. The carbon content of this steel type sits at between 0.3 and 0.6% and the steel itself is usually further treated with austenitizing (a type of heat treatment), quenching and then tempering the metal for the sake of stronger mechanical properties.
Medium steel is usually used in its tempered condition because this state gives it internal microstructures of tempered martensite for a powerful balance between ductility and high strength. Medium carbon steel is usually made with alloys such as chromium, nickel and molybdenum. It’s especially popular for uses where exceptional strength and wear resistance need to balance with some ductility. These applications include:
- Large machine components
- Gears and axles
- Forgings
- Machined tools
- Railway wheels
- Machinery shafts
Low Carbon Steel
Also known as mild or plain carbon steel, low carbon steels contain between 0.05% and 0.3% carbon content and manganese levels that vary between 0.4% and 1.5%. At the extreme lower end of this carbon percentage spectrum, the mild steel blend with the least amount of carbon is technically referred to as wrought iron, at 0.05 to 0.1% carbon. Just like cast iron with its extremely high carbon content of around 2%, very-low carbon wrought iron has limited uses .
When its carbon content is raised, mild steel becomes a highly tensile product. This means a lower percentage of carbon content for high ductility. But it also includes alloying the metal with other metals like chromium, molybdenum, silicon, manganese, nickel, and vanadium. The addition of these elements increases low carbon steel’s tensile strength so that it can be widely used in all sorts of industrial, commercial and construction scenarios.
In other words, low carbon steels enjoy quite a wide range of applications, such as in:
- The automotive industry (in the form of tailgate access covers, floor pans, roofs, hoods, doors, and body sides, spare tire tubs, dash panels, etc.)
- Wire products
- Tin plate
- Building panels
- Beams and other structural materials
- Sprocket assemblies
- Fasteners
- Bolts
- Fences
- Chain links
- Gates
- Railings
Pros and Cons
In general, carbon steels are great for their durability, strength, and shock resistance. This makes them cheaper to use than other steels because relatively fewer quantities are needed for a given application. They are also easier—and thus cheaper—to recycle than other steels. However, carbon steel of all grades tends to be more easily affected by corrosion than other steels, so their maintenance is much more labor- and time-intensive.
High Carbon and Ultra-high Carbon Steel
These steels can undergo heat treatment and tempering. In fact, this is one of their most desirable qualities, and they are highly sought after by knife and sword makers for their ability to take and hold an edge.
However, high carbon steels tend to be much more expensive and harder to work with than low and medium carbon steels. Thus, the techniques and technology needed to work with them are somewhat more specialized and costly.
Low Carbon Steel
These steels are some of the most common and readily available due to their low production costs and relative ease of manufacture. Their physical properties also make them well suited to a wide array of applications. For instance, they are much more malleable and ductile than high carbon steels and are much easier to machine.
Low carbon steels are also much more conducive to applications that require welding than medium or high carbon steels. This is directly because of the carbon content. As its presence increases, the carbon in steel makes it more susceptible to hardening. This is a pro application in which hardness is desired, but it increases the likelihood of cracking in applications that require welding and are thus subject to higher amounts of stress for longer durations.
However, while low carbon steels display a great deal of strength and toughness, they tend to refuse tempering, and so cannot be made as hard as higher carbon content steels.
Do You Need Carbon Steel for Your Next Project?
Congratulations, you can now consider yourself fully informed about the differences between high carbon steel vs low carbon steel! But as a construction company owner, contractor, or purchasing coordinator, you may yet be wondering where you can get your hands on building materials made of the stuff.
Luckily for you, Bushwick Metals offers a vast array of products made of high-quality structural steel. They are readily available to clients all over the eastern US, and we even offer next-day shipping to most states!
When you’ve decided what you need for your next project, don’t hesitate to reach out to us. In fact, you can request a quote right here!